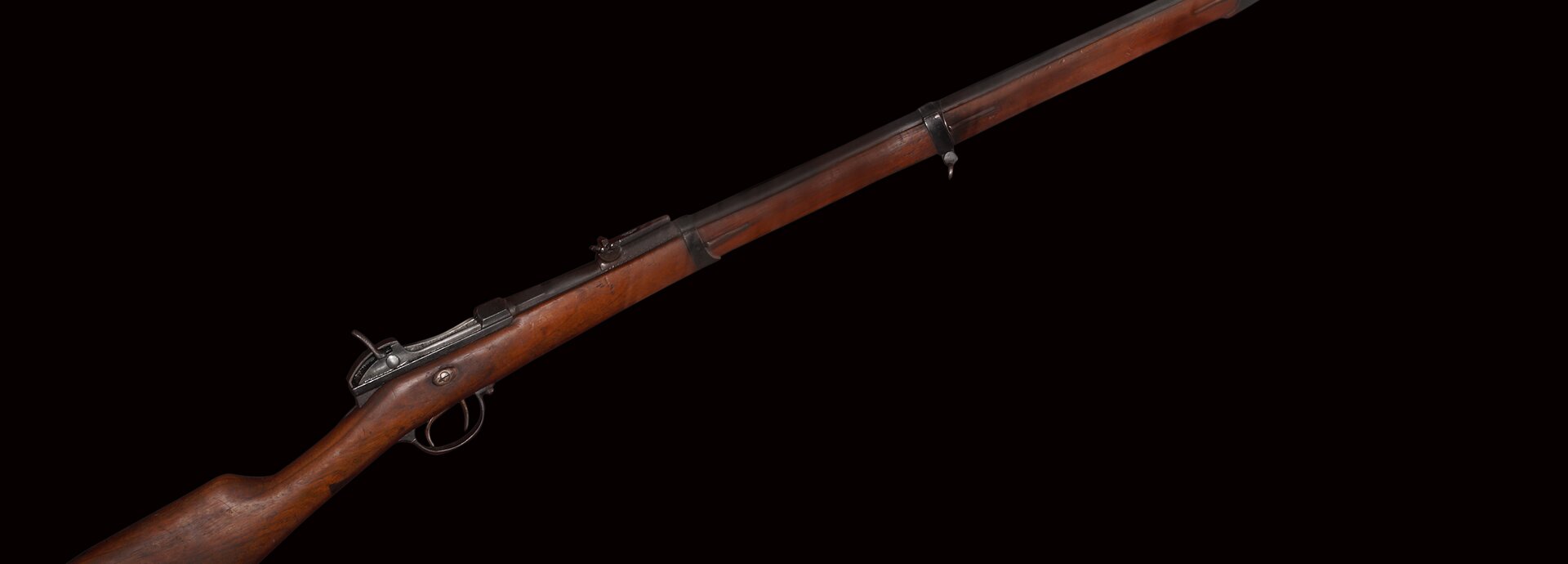
11/11/2024 | Hints from the experts
Vetterli rimfire cartridges for Milbank-Amsler and Peabody rifles
The Vetterli rimfire cartridge was later developed into a centre-fire cartridge. With cases correctly sized and trimmed to length, these cartridges will of course chamber in vintage Milbank-Amsler and Peabody rifles from 1867. However, these centre-fire cartridges will not fire in either rifle, as both are designed for rimfire cartridges and must therefore be converted first.
Accordingly, if you wish to shoot an original Milbank-Amsler or Peabody rifle, then you will need to manufacture suitable rimfire cartridges that can be reloaded, if possible. The following images show a Milbank-Amsler and a Peabody rifle with chambered rimfire cartridges. The cases have been converted so that the firing pin strikes a 6-mm blank cartridge.
50-110 Win or 348 Win cases from Starline Inc. (1300 Henry, Sedalia, Missouri, 65301, USA) are suitable as a basis for manufacturing cartridges like these. For this article, I used the 50-110 Win, since I have already been using this case for a Vetterli and a Peabody rifle that have been converted to centre-fire. The head and rim of these cases are very similar to the original Vetterli cartridge. The converted cases can be reloaded about 20 times before developing cracks in the neck area.
To ensure the bullet sits better in the case, I extended the case length to 42 mm, which proved to be successful when shooting.
For sizing, I use a die kit in calibre 41 Swiss from Lee Precision, Inc (4275 Country Road U, Hartford, WI 53027, USA). For the projectile, I use hard-cast lead bullets (BH 10.4) weighing 15 g (231 grains), comparable to bullets cast using a Lee 429-240-2R mould. All bullets are calibrated to 10.75 mm.
The individual steps involved in manufacturing the cases are described in the following. In addition to standard DIY tools, I used a lathe, but the same results can be achieved without one.
The image below shows 50-110 Win calibre cases, brass screws used to seal the primer pocket and flash hole, and a finished and resized case converted to rimfire.
To start, trim the case to a length of 42 mm. Next, bore out the primer pocket and flash hole in the case head to 4 mm and tap an M5 thread into the bore.
Screw an M5 brass screw into the thread from the inside of the case and tighten it securely. I used cross-recessed pan-head screws, as they are easy to hold on the tip of a screwdriver. Of course, other M5 brass screws can be used as well. Figure 7 shows the work steps completed to this point.
In the next step, solder the brass screw to the case using soft solder. In preliminary tests, I brazed the screws but found that the heat caused the case heads to become soft. Internet sources claim that the brass screws can be bonded using adhesive. However, I doubt that an adhesive bond would withstand the forces that are generated when the cartridge is fired. I therefore do not recommend this either.
Next, remove the protruding thread and solder so that the case head is flat. You can do this on a lathe, or a saw and file will work just as well. Next, size the case to its specified dimensions. Since the case expands in length slightly during sizing, trim it to a length of 42 mm afterwards. It is not sensible to perform this step prior to soldering, as the heat generated during soldering will cause the case head to expand slightly, which would then require resizing. Caution: During sizing, ensure that the decapping pin on the die, which is designed to push out the spent primer of a centre-fire case, does not come into contact with the case head, otherwise it could break or be bent.
The 6-mm rimfire blank cartridges are approx. 5 mm long, 5.7 mm in diameter at the case head, and have a rim with a diameter of just under 7 mm that is approx. 0.5 mm thick. The seating for the blank cartridge must be fabricated so that the cartridges have a straight fit in the case.
Next, drill a bore into the case head using a 4-mm metal drill bit. The bore should contact the inner wall of the case in a straight line so that the case head is not weakened. This 4-mm bore serves as the blank cartridge’s flash hole to the main powder charge in the case. Next, fabricate the seating for the blank cartridge. Use a 5.7-mm metal drill bit to bore out the 4-mm bore to a depth of 5 mm. Boring any deeper would weaken the case head too much.
Now use a 7-mm metal drill to widen the seat to a depth of approx. 0.6 mm and create a counterbore for the rim of the blank cartridge.
Finally, working from above, use a file to drop the case rim by approx. 0.6 mm to prevent the firing pin of the Milbank-Amsler or Peabody rifle from striking it. If the case is to be fired from a Vetterli rifle, also file away or make a notch in the opposite side of the rim to create space for the second pin of the forked firing pin.
The blank cartridges may drop out of the cases easily. I use a glue stick to secure them in their seating. This is sufficient to keep them in place, and they can still be popped out easily before resizing.
All work steps are summarised in the following.
The cases are now ready. I charged them with 1.68 g (26 grains) of powder using a 1.3-ccm dipper. Since the cases are only partially filled, I topped the charges with a tuft of cotton swab.
Trial shots exhibited a muzzle velocity of 430 m/s. The simulations by Mr Dominik Antenen using an Italian 10.4 × 47 Vetterli and a 40-65 Win case charged with 1.68 g (26 grains) of RS 36 exhibited a muzzle velocity of approx. 450 m/s (1,450 fps) and a pressure of approx. 650 bar (9,450 psi). This is pretty similar to my own measurements of muzzle velocity. The pressure corresponds to approx. 50% of the maximum specified for Vetterli rifles and should also fall within the permissible pressure range for Milbank-Amsler or Peabody rifles. For black powder loads, literature indicates approx. 1,400 bar (20,000 psi) for these rifles.
I would like to emphasise once again that every shooter is responsible for the conversion of firearms and/or cartridges and the loading of their own cartridges and that I accept no responsibility for the loading data, information and results presented here.
Best regards,
U. Daum
Hallau, 23 September 2024